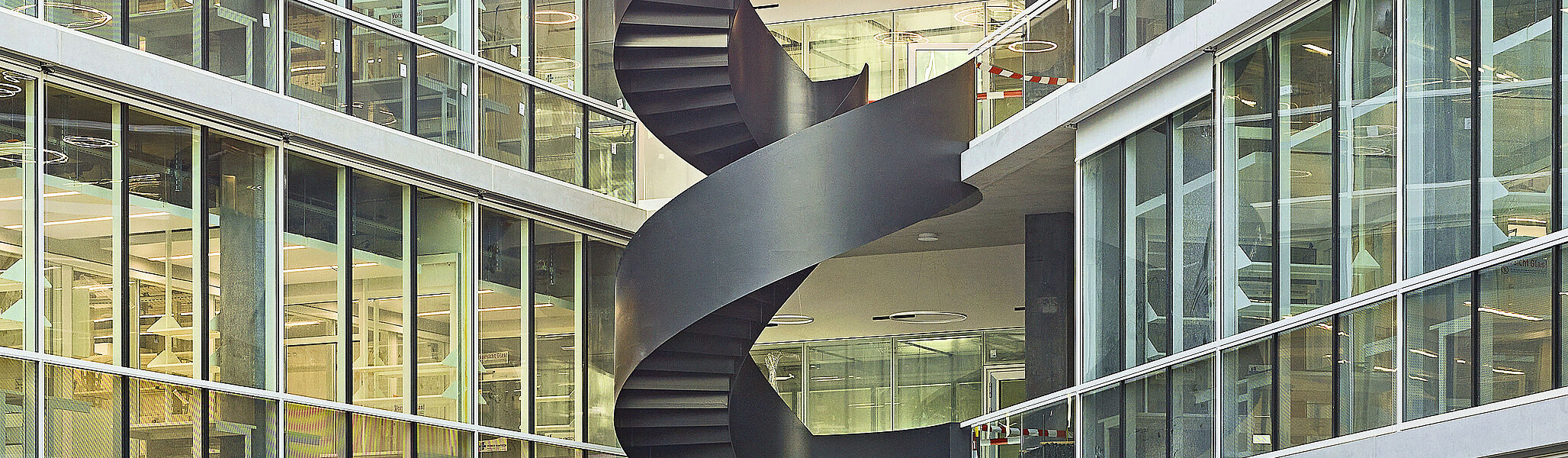
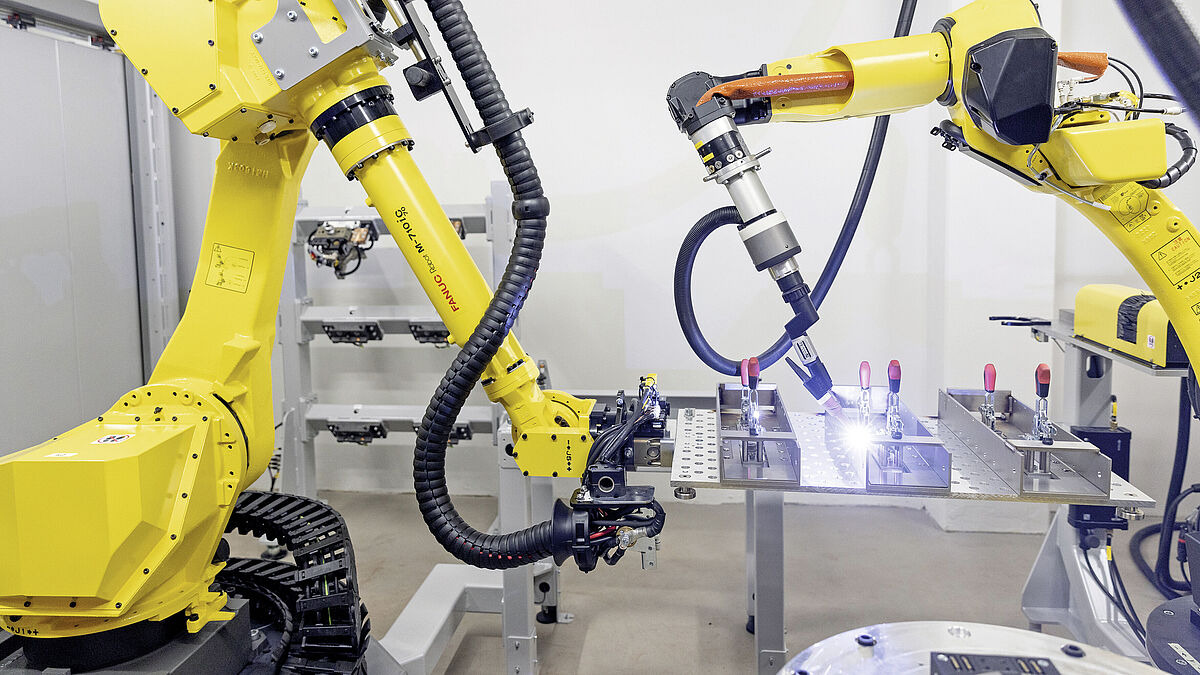
Fit für die Zukunft dank smarter Roboterschweisstechnik
Schweissen
Fortschritt und Innovation im Dialog mit dem Kunden: Das österreichische Vorzeigeunternehmen Anton Paar fertigt hochpräzise Messgeräte für vielerlei Branchen. Dabei ist es der Anspruch der engagierten Forschungs-, Engineering- und Fertigungsteams, die Grenzen des Machbaren immer weiter zu verschieben. Heute ist die Anton Paar GmbH Weltmarktführer bei Dichte- und Konzentrationsmessung, Rheometrie sowie der Bestimmung von gelöstem CO 2 . Da zunehmender Fachkräftemangel und permanent steigende Stückzahlen intelligente Produktionslösungen erfordern, investierte das Unternehmen in eine Roboterschweisszelle der neuesten Generation. (Text in gekürzter Fassung)
Login
Danke für Ihr Interesse an unseren Inhalten. Abonnenten der Fachzeitschrift metall finden das Login für den Vollzugriff im Impressum der aktuellen Printausgabe. Das Passwort ändert monatlich.
Jetzt registrieren und lesen. Registrieren Sie sich um einzelne Artikel zu lesen und einfach per Kreditkarte zu bezahlen. (CHF 5,- pro Artikel)
Als registrierter Benutzer haben Sie jederzeit Zugriff auf Ihre gekauften Artikel.
Sollten Sie als interessierte Fachkraft im Metall-, Stahl- und Fassadenbau die Fachzeitschrift metall tatsächlich noch nicht abonniert haben, verlieren Sie keine Zeit und bestellen Sie Ihr persönliches Abonnement gleich hier.
Schweissen
Fit für die Zukunft dank smarter Roboterschweisstechnik
Fortschritt und Innovation im Dialog mit dem Kunden: Das österreichische Vorzeigeunternehmen Anton Paar fertigt hochpräzise Messgeräte für vielerlei Branchen. Dabei ist es der Anspruch der engagierten Forschungs-, Engineering- und Fertigungsteams, die Grenzen des Machbaren immer weiter zu verschieben. Heute ist die Anton Paar GmbH Weltmarktführer bei Dichte- und Konzentrationsmessung, Rheometrie sowie der Bestimmung von gelöstem CO 2 . Da zunehmender Fachkräftemangel und permanent steigende Stückzahlen intelligente Produktionslösungen erfordern, investierte das Unternehmen in eine Roboterschweisszelle der neuesten Generation. (Text in gekürzter Fassung)
Bisher wurden sämtliche Komponenten der in Graz produzierten Mess- und Regelgeräte händisch geschweisst. Der Grund: Kleine Losgrössen zwischen 1 und 400 Stück liessen Roboterschweissanlagen unwirtschaftlich erscheinen. Ständige Umsatzzuwächse, der steigende Fachkräftemangel auf dem inländischen Arbeitsmarkt sowie innovative Robotertechnologien – die mittlerweile automatisiertes Schweissen auch bei kleinen Losgrössen wirtschaftlich machen – veranlassten das Hightech-Unternehmen, in eine moderne Roboterschweissanlage zu investieren. Flexibilität auf allen Linien in Kombination mit hoher Wirtschaftlichkeit lautete dabei die Vorgabe der Mess- und Regelspezialistinnen und -spezialisten: Flexibilität bei Anzahl, Form und Grösse der Bauteile, bei deren Positionierung und beim Einsatz unterschiedlicher Schweissverfahren.
Dominik Santner, COO der Anton Paar GmbH, betont: «Fachkräftemangel und kontinuierlich steigende Stückzahlen erfordern zukunftsorientierte Lösungen in der Produktion. Die neue Roboterschweisszelle ist ein grosser Schritt in der Automatisierung unserer Fertigung. Würden wir unsere Prozess-Sensorik nach wie vor manuell schweissen, hätten wir in den kommenden Jahren enorme Schwierigkeiten, die geplanten Stückzahlen zu erreichen.»
Schweissautonomie und Vielfalt bei Bauteilen
Von Anfang an setzten die Expertinnen und Experten von Anton Paar auf Anlagenautonomie: Einmal gerüstet, sollte das Schweisssystem einen kompletten Auftrag vom Anfang bis zum Ende in einem Zug abwickeln können – zum Beispiel das Schweissen einer Charge unterschiedlicher Objekte wie Schwingergehäuse, Hauptträger oder Gegenkühlungen. Dies sollte völlig selbständig und ohne Eingreifen von Schweissfachkräften möglich sein.
Unterschiedliche Bauteile in Form, Gewicht und Grösse, verschiedene Greif-, Positionierungs- und Ablagemöglichkeiten, die Option, bei einer Komponente zwei verschiedene Schweissverfahren (WIG und MIG/MAG) zum Einsatz zu bringen, sowie der bei zylindrischen Körpern notwendige Einsatz von Formiergas zum Schutz der Bauteile gegen Anlauffarben – all das machte die Konstruktion der Anlage für Ingenieur- und Programmierteams zu einer besonderen Herausforderung.
«Wir suchten einen verlässlichen Partner, der uns bei Präzision und Qualität sehr ähnlich ist. Er sollte uns wirklich zuhören, auf unsere Wünsche eingehen und zukunftsfähige Lösungen vorschlagen. Solche, die uns auf Jahre hinaus Wettbewerbsvorteile verschaffen», erklärt Daniel Moik, Department Manager Joining Technologies. «Fronius International erfüllte diese Vorstellungen von einer nachhaltigen Partnerschaft. In enger Zusammenarbeit mit unseren Technikern entwickelte das Team der Welding Automation eine Roboterschweisszelle, die unseren Anforderungen in allen Punkten gerecht wird. Obendrein ist man bei Fronius bereit, die Anlage gemeinsam weiterzuentwickeln und auf neue Bedürfnisse abzustimmen.»
«Wir suchten einen verlässlichen Partner, der uns bei Präzision und Qualität sehr ähnlich ist. Er sollte uns wirklich zuhören, auf unsere Wünsche eingehen und zukunftsfähige Lösungen vorschlagen. Solche, die uns auf Jahre hinaus Wettbewerbsvorteile verschaffen.»
Synonym für Effizienz: Fronius Pathfinder
Neue Schweissnähte werden bei Anton Paar offline – abseits vom Schweisssystem – programmiert, nicht wie häufig üblich unmittelbar an der Anlage. Anstatt laufende Schweissarbeiten zu stoppen, wird weitergeschweisst und auf diese Weise die Produktivität gesteigert. Um das zu ermöglichen, importieren die Schweisstechnikerinnen und -techniker die CAD-Daten der zu schweissenden Messgerätekomponenten in den Fronius Pathfinder. Anschliessend werden verschiedene Fügeszenarien getestet, Schweissfolgen definiert und im Zuge von Simulationen optimiert.
Betroffen sind Anfahrtswege, Brenner-Anstellwinkel, Brenner-Offsets in den Eckbereichen und sämtliche Umorientierungen des Schweissroboters. Überschreitungen der Roboterreichweite, sogenannte Achslimits, werden vom Pathfinder erkannt. Indem die Softwarebedienerinnen und -bediener den Ablageort des Werkstücks korrigieren und es innerhalb der Armlänge des Schweissroboters in Position bringen, werden potenzielle Kollisionen des Brenners mit diversen Bauteilkanten frühzeitig vermieden.
Fehlerquellen werden rechtzeitig erkannt
Sind Bahnkorrekturen notwendig, können die betroffenen Teach-Punkte bequem per Drag-and-drop verschoben werden. Soll eine Anfahrt zum Bauteil geändert werden, drücken die Fachkräfte kurzerhand «Reset». In der Folge fährt der virtuelle Roboter zum Start einer neuen Anfahrt in die Home-Position. Im Realbetrieb müsste man den Roboter zeitaufwendig freifahren, mittels Robotersteuerung in die Home-Position bewegen und den Teach-Vorgang neu starten. Indem sich die Expertinnen und Experten von Anton Paar für die Offline-Programmier- und Simulationssoftware Pathfinder entschieden haben, gewinnen sie nicht nur wertvolle Zeit für Schweissarbeiten, sondern erkennen Fehlerquellen bereits im Vorfeld.
Sobald ein Schweissprogramm im Pathfinder fertiggestellt ist, wird es von einem sogenannten Postprozessor in den spezifischen Code des Fanuc-Schweissroboters übersetzt. Jetzt kann es per Datentransfer – zum Beispiel mit einer LAN-Verbindung – in die Schweissanlage übertragen werden. Ein besonderes Highlight und eine effektive Unterstützung der gesamten Produktionsplanung ist die Funktion «Taktzeitermittlung», die Schweissgeschwindigkeiten, Gasvorström- oder Endkraterfüllzeiten einbezieht. Im Vergleich zum Teachen mit der Robotersteuerung lassen sich mit dem Pathfinder – abhängig von der Bauteilgeometrie und den schweisstechnischen Anforderungen – bis zu 90 % Zeitersparnis erzielen.
Massgeschneidert
Für das Schweissen der vielen unterschiedlichen Bauteile stehen Anton Paar kundenspezifische Workflows zur Verfügung, darunter die drei Hauptworkflows, die die enorme Flexibilität beim Bauteilspektrum beispielhaft veranschaulichen.
Workflow 1: Die Bauteile werden auf dem Dreh-Kipp-Positionierer geschweisst. Dabei wird eine mit Bauteilen bestückte Palette aus dem Palettenregal entnommen und auf einem Palettenablagetisch zwischengelagert. Im weiteren Verlauf rüstet der Handling-Roboter einen passenden Greifer für die Bauteilaufnahme, wobei sechs verschiedene in einem sogenannten Greiferbahnhof stationiert sind. Damit ausgestattet, nimmt der Handling-Roboter die Bauteile auf und fixiert sie in einer bauteilspezifischen Spannvorrichtung, die bereits auf dem Dreh-Kipp-Tisch aufgerüstet ist. Es wird immer ein Bauteil nach dem anderen entnommen, gefügt und wieder auf die Palette zurückgelegt.
Workflow 2: Die Bauteile werden unmittelbar auf den Paletten geschweisst, wobei der Handling-Roboter die Paletten aus dem Palettenregal transportiert und vor dem Schweissroboter positioniert. Beim Schweissen können dann Handling- und Schweissroboter gemeinsam koordinierte Bewegungen ausführen und deshalb nicht nur einfache, sondern auch komplexe Nahtgeometrien schweissen.
Workflow 3: Die Bauteile werden einzeln entnommen, vom Handling-Roboter in Position gebracht und bewegen sich beim Schweissen synchron mit dem Schweissroboter (Coordinated Motion).
Damit die Anlage weiss, was zu tun ist
Abgesehen von der innovativen Fronius-Schweisstechnologie, den Steuerungen, der Tool-Center-Point(TCP)-Vermessung, der Brennerreinigungsstation und der Einhausung besteht die Roboterschweissanlage aus sieben Kernmodulen, die softwaregesteuert kollaborieren: einem Handling-Roboter, einem Schweissroboter, einem Dreh-Kipp-Positionierer mit Formiergaseinheit, einem Palettenlager mit zwei Regalen, einem Greiferbahnhof, einem Brennerwechselsystem und einer Palettenablage im Inneren der Anlage.
www.fronius.com
Den ganzen Text finden Sie hier ■