
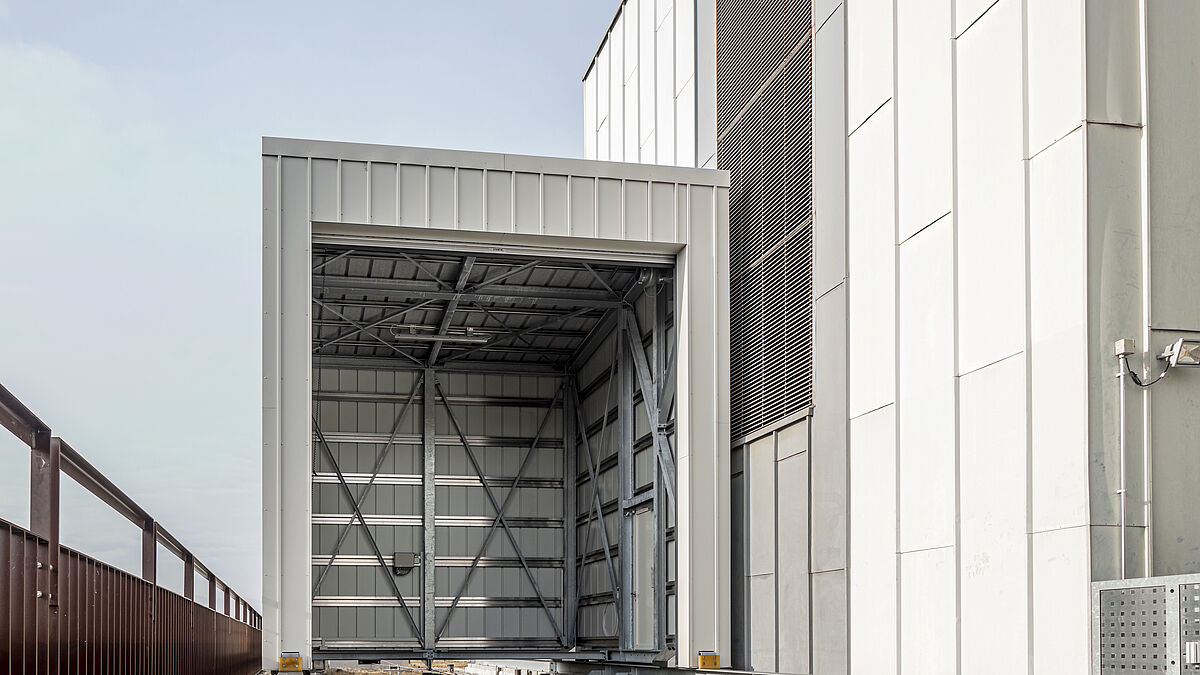
Fahrbare Garage schützt den Parabolspiegel
Stahlbau
An der ETH Zürich wurde eine Technologie entwickelt, die aus Sonnenlicht und Luft flüssige Treibstoffe herstellt. Als zentrales Element hierfür dient ein Parabolspiegel auf dem Dach der ETH. Um das sensible Instrument bei Nichtgebrauch vor Witterungseinflüssen zu schützen, wurde eine auf Schienen gelagerte, fahrbare Garage gebaut. Stahl, Mechanik, Elektronik und Innovation spielten dabei eine zentrale Rolle.
Login
Danke für Ihr Interesse an unseren Inhalten. Abonnenten der Fachzeitschrift metall finden das Login für den Vollzugriff im Impressum der aktuellen Printausgabe. Das Passwort ändert monatlich.
Jetzt registrieren und lesen. Registrieren Sie sich um einzelne Artikel zu lesen und einfach per Kreditkarte zu bezahlen. (CHF 5,- pro Artikel)
Als registrierter Benutzer haben Sie jederzeit Zugriff auf Ihre gekauften Artikel.
Sollten Sie als interessierte Fachkraft im Metall-, Stahl- und Fassadenbau die Fachzeitschrift metall tatsächlich noch nicht abonniert haben, verlieren Sie keine Zeit und bestellen Sie Ihr persönliches Abonnement gleich hier.
Stahlbau
Fahrbare Garage schützt den Parabolspiegel
An der ETH Zürich wurde eine Technologie entwickelt, die aus Sonnenlicht und Luft flüssige Treibstoffe herstellt. Als zentrales Element hierfür dient ein Parabolspiegel auf dem Dach der ETH. Um das sensible Instrument bei Nichtgebrauch vor Witterungseinflüssen zu schützen, wurde eine auf Schienen gelagerte, fahrbare Garage gebaut. Stahl, Mechanik, Elektronik und Innovation spielten dabei eine zentrale Rolle.
An idealer Lage, auf dem Flachdach der ETH Zürich und somit frei von lichteinschränkenden Nachbarsbauten, thront der neue Parabolspiegel, der die Solarstrahlung konzertiert dem Solarreaktor als Prozesswärme zuführt, um schliesslich flüssige Treibstoffe zu gewinnen (siehe auch «Technische Information» im Anhang). Das hochsensible Gerät weist einen Durchmesser von rund 2 m auf und gilt als höchst gelenkig. Damit der sich bewegende Spiegel in jeder Ausgangsstellung stabil steht, ist er auf eine massive Plattform aus Stahl abgestellt.
Zum Schutz vor Wind und Wetter baute die Blaser Metallbau AG, Andelfingen, eine fahrbare Garage von 5 m Breite, 5 m Tiefe und ebenfalls 5 m Höhe. Den Abschluss dieses voluminösen Gewerks bildet ein integriertes Rolltor. Für den seitlichen Zugang ist eine Einflügeltüre eingebaut. Alle Abschlüsse sind mit entsprechenden Sicherheitsvorkehrungen und Überwachungselementen ausgestattet.
Zwölf Tonnen fahren auf Schienensystem
Um den Parabolspiegel den solaren Strahlen auszusetzen, muss dieser zuerst von der schützenden Einhausung befreit werden. Hierfür wird das Rolltor geöffnet, die Sicherungselemente gelöst, und die im Grundriss U-förmige Einhausung kann mit Hilfe des elektrisch betriebenen Seilzugs auf dem Schienensystem weggefahren werden.
Die Tragkonstruktion dieser fahrbaren Garage besteht aus Breitflanschträgern und Formstahl-Profilen. Ein dreiseitig umlaufender Bodenrahmen mit darauf aufgeständerten Stahljochen – in Kombination mit diversen Windverbänden – bildet das primäre Tragwerk. Aussenseitig angebrachte, horizontal verlaufende Aluminiumprofile dienen als Unterkonstruktion für die vertikal geführten Paneelbleche vom Typ Montaform 25/333. Gesamthaft bringt die fahrbare Konstruktion rund 12 Tonnen Gewicht auf die Schienen.
Ziel der Entwicklung war es, eine möglichst leichte, aber windstabile Kabine zu bauen. Dabei galt es, in statischer Hinsicht die unterschiedlichen Wind-, Wetter - und Temperaturverhältnisse, die über das ganze Jahr hinweg in der Stadt Zürich herrschen, zu berücksichtigen. Dies für das Gehäuse ebenso wie für das Rolltor und auch für sämtliche mechatronischen Komponenten.
Elektromotor sorgt für Bewegung
Die Kabine fährt auf einem rund 28 m langen Schienensystem aus Walzprofilen HEA 260 beinahe geräuschlos an ihren Zielort. Unten angebrachte Schwerlastrollen aus Polyamid, mit einem Durchmesser von 150 mm und einer Stärke von 50 mm, gewähren eine Tragfähigkeit von 2100 kg pro Rad und ermöglichen so eine reibungsfreie Fahrt.
Angetrieben über einen Seilzug mit Umlenkvorrichtung und Elektromotor, bewegt sich die Kabine rund 20 m in 3 Minuten. Die Entwicklung der Antriebseinheit erfolgte in Zusammenarbeit mit der Firma Wyss Bühnenbau AG, Näfels. Der Elektromotor mit Getriebe dreht die Seiltrommel, das Seil wird gleichzeitig auf- bzw. abgewickelt. Die genaue Positionierung wird mit Hilfe von Annäherungssensoren erreicht. Als Endsicherung dient ein mechanischer Auflaufbock. Die Betätigung der Antriebseinheit erfolgt über eine Totmann-Steuerung und im Winter sorgt ein Schneeräumschild vor den Rädern für den sicheren Betrieb.
Viele technische Herausforderungen
«Im Zuge der Entwicklung dieser fahrbaren Konstruktion hatten wir einige technische Hürden zu nehmen», erklärt Daniel Vonrüti, CEO bei der Blaser Metallbau AG, «dazu gehörte die Erfüllung aller technischen Anforderungen der ETH, auch an die Mechatronik. Dies im Zusammenhang mit den elektrisch erschlossenen Komponenten wie Rolltor, Servicetüre, Antriebstechnik und einiges mehr. Parallel dazu galt es auch, die notwendigen Schutzmassnahmen zu erfüllen und Maschinenrichtlinien inklusive CE-Kennzeichnung einzuhalten. Natürlich bildeten auch die entsprechenden Dokumentationen einen Bestandteil.
Aber auch das enge Zeitfenster für den Gesamtprozess – von der Planung über die Herstellung bis und mit Montage – machte dieses Projekt zu einer spannenden Angelegenheit. Die Montage selbst forderte viel Innovationsgeist und exakt vordefinierte Abläufe.»
Montage – eine logistische Herausforderung
Um den künftigen hohen Belastungen standzuhalten, musste zuerst das bestehende Dach umgebaut und entsprechend saniert werden. Die gewichtige und sich bewegende Stahlkonstruktion benötigte massive Betonfundamente, die vor Ort gegossen wurden. Die Montage selber war dann geprägt von den sehr engen Platzverhältnissen, einerseits für die Zubringung der Materialien, andererseits auch für die eigentlichen Installationen der Bauteile. So liess Blaser für die Anlieferung der Materialien einen selbstaufstellenden Schnelleinsatzkran installieren. Dadurch konnte auf länger anhaltende Strassensperrungen verzichtet werden und die räumliche Überbrückung von rund 60 m – hinweg über bestehende Oberleitungen der Tramlinien – gelang auch bestens. Die Anlieferung der Materialien erfolgte minutiös geplant, den Platzverhältnissen und dem Montageablauf entsprechend. Für die Aufrichtung des Stahlbaus und die weiteren Installationen kam ein mobiler Miniraupenkran zur Anwendung.
Da während der Montage das gesamte Gebäude der ETH in Betrieb war, mussten Lärmemissionen so gut wie nur möglich vermieden werden. Und nicht zuletzt: Während der sommerlichen Montagephase herrschten auf dem frisch isolierten Dach, belegt mit dunklen Folien, Temperaturen von über 40 °C, die doch wesentlich über das Angenehme hinaus gingen. ■
Bautafel
Objekt:
ETH Zürich
Bauherrschaft:
ETH Zürich
Architektur und Bauleitung:
Itten + Brechbühl AG, Zürich
Stahl- und Metallbau:
Blaser Metallbau AG, Andelfingen
Partner Antriebstechnik:
Wyss Bühnenbau AG, Näfels
Technische Information (Quelle ETH Zürich)
Forschende der ETH Zürich haben die Technologie entwickelt, die aus Sonnenlicht und Luft flüssige Treibstoffe herstellt. Zum ersten Mal weltweit demonstrieren sie die gesamte thermochemische Prozesskette unter realen Bedingungen mit der solaren Mini-Raffinerie auf dem Dach des Maschinenlaboratoriums der ETH Zürich.
Funktion der neuen solaren Mini-Raffinerie
Die Prozesskette der neuen Anlage integriert drei thermochemische Umwandlungsprozesse: erstens die Abscheidung von CO 2 und Wasser aus der Luft, zweitens die solar-thermochemische Spaltung von CO 2 und Wasser und drittens die anschliessende Verflüssigung in Kohlenwasserstoffe. Durch einen Adsorption-Desorption-Prozess werden CO 2 und Wasser direkt aus der Umgebungsluft entnommen. Beides wird dem Solarreaktor im Fokus eines Parabolspiegels zugeführt.
Die Solarstrahlung wird durch den Parabolspiegel 3000-mal konzertiert, im Innern des Reaktors eingefangen und in Prozesswärme mit einer Temperatur von 1500 °C umgewandelt. Im Herzen des Reaktors befindet sich eine spezielle keramische Struktur aus Ceriumoxid. Dort werden in einer zweistufigen Reaktion – dem sogenannten Redox-Zyklus – Wasser und CO 2 gespalten und Syngas hergestellt. Die Mischung aus Wasserstoff und Kohlenmonoxid kann mittels konventioneller Methanol- oder Fischer-Tropsch-Synthese in flüssige Treibstoffe weiterverarbeitet werden.