
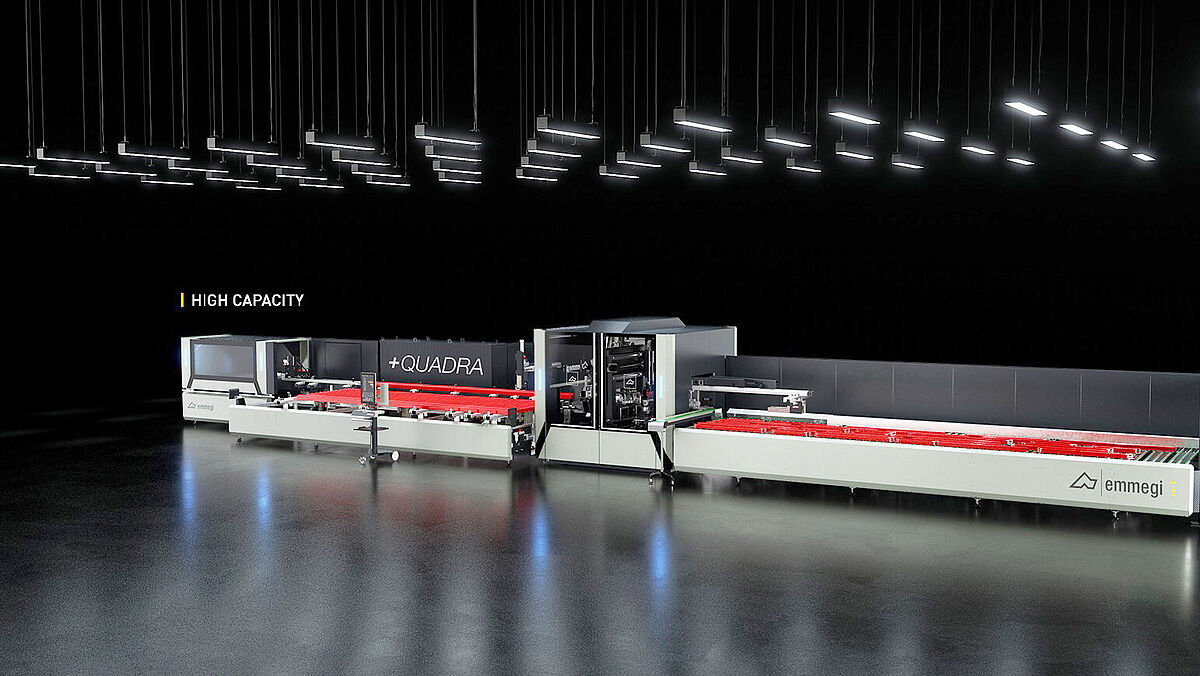
Traitement automatisé de profilés
Machinerie / Traitement de profilés
L’industrialisation et l’automatisation de la construction métallique et de façades se sont progressivement développées au cours des dernières années. Poussées par la vague actuelle de numérisation, de plus en plus d’entreprises suisses de construction métallique et de façades planifient les prochaines étapes menant à l’usinage autonome des profilés.
Connexion
Merci de l’intérêt que vous portez à nos contenus. Les abonnés de la revue spécialisée metall trouveront le Login pour l’accès intégral dans les informations légales de la version imprimée actuelle. Le mot de passe change tous les mois.
Inscrivez-vous maintenant pour lire cet article. Inscrivez-vous pour lire les différents articles et payez très facilement par carte de crédit. (CHF 5.- par article)
En tant qu’utilisateur enregistré, vous pouvez accéder à tout moment à l’article acheté.
Si - en tant que professionnel dans les domaines de la construction métallique, en acier et de façades - vous n’êtes pas encore abonné à la revue spécialisée metall, ne perdez plus une seconde et souscrivez dès à présent votre abonnement ici.
Machinerie / Traitement de profilés
Traitement automatisé de profilés
L’industrialisation et l’automatisation de la construction métallique et de façades se sont progressivement développées au cours des dernières années. Poussées par la vague actuelle de numérisation, de plus en plus d’entreprises suisses de construction métallique et de façades planifient les prochaines étapes menant à l’usinage autonome des profilés.
Les solutions proposées pour les fabrications à commande numérique industrielles ne peuvent toutefois pas être simplement copiées, car les secteurs d’application et les dimensions des matériaux sont trop différents. Les grandes séries font souvent défaut. La taille de lot unitaire est plutôt la norme. Les angles, les longueurs, les usinages et les séries de profilés changent constamment.
Exigences actuelles
Dans le pays à hauts salaires qu’est la Suisse, la réduction des effectifs est un argument important en faveur de l’automatisation, mais ce n’est pas le seul. L’espace souvent restreint exige un stockage intermédiaire aussi réduit que possible de produits semi-finis. Toute manipulation supplémentaire est en outre associée à des risques d’erreur.
Le souhait d’une équipe de nuit aussi longue que possible et la réduction de la durée d’usinage (de la réception des commandes à l’achèvement des pièces) sont d’autres exigences qui pèsent sur les centres d’usinage de profilés, qui ont considérablement progressé ces dernières années.
Dans la fabrication à commande numérique classique, les machines neuves et existantes sont automatisées à l’aide de robots ou de cellules de fabrication Cobot. Les petites pièces et zones de travail le permettent souvent sans interface logicielle ni interventions importantes.
Dans l’usinage de profilés, il faut couvrir des matériaux de départ d’une longueur de 6 m ainsi que des produits finis très variables. Lors de l’équipement de grands portiques, cette approche requiert des solutions d’automatisation très importantes et complexes.
Séparation, première étape de l’automatisation
L’étape d’automatisation associée à une séparation est très répandue sur les machines 5 axes depuis des années. Une barre est posée et les pièces finies sont retirées ultérieurement. La machine fonctionne ainsi plus longtemps sans opérateur. Cette fonction relève de la norme chez Emmegi Tekna. Elle est disponible sur tous les centres d’usinage 5 axes.
Les coûts de découpe sur une machine à 5 axes sont évidemment plus élevés que sur une scie à double onglet, mais ils peuvent généralement être compensés par la suppression d’étapes de travail et de surfaces de stockage.
Deuxième étape : un centre d’usinage comme solution d’automatisation
Les centres d’usinage de profilés en continu disposent d’une automatisation à l’intérieur de la machine grâce aux magasins de chargement et de déchargement.
Plus de 600 centres d’usinage de type Quadra sont déjà utilisés dans le monde entier pour la production en grands volumes. Le principe de l’usinage en continu présente des avantages évidents par rapport aux modèles classiques à une barre. Des augmentations de débit supérieures à 40 % sont possibles selon le type d’usinage. Le chargement et le déchargement de la machine s’effectuent en temps réel, de telle sorte que l’outil reste en grande partie en action.
Contrairement au fraisage à commande numérique classique, l’usinage de profilés produit des goussets et des restes qui ne sont pas entièrement réduits en copeaux. L’espace d’usinage de l’Emmegi Quadra est optimisé pour leur élimination et garantit la sécurité de processus nécessaire pour le traitement fiable des longues phases sans opérateur.
La nouvelle version de l’Emmegi +Quadra offre des possibilités supplémentaires visant à augmenter considérablement ces périodes d’autonomie. Une nouvelle unité de chargement permet de stocker plus de profilés sur la même surface. En combinaison avec un magasin de déchargement haute capacité, les pièces fabriquées à partir de celui-ci peuvent également être déchargées automatiquement sans intervention manuelle. Toute la surface du magasin de déchargement est utilisée de manière optimale. De plus, l’application d’une étiquette peut désormais s’effectuer de manière entièrement automatique dans la machine sur trois faces du profilé, ce qui permet de minimiser les temps morts lors du débarrassage de l’unité d’élimination ainsi que les confusions.
Par le passé, l’impossibilité d’usiner la face avant comme sur des centres d’usinage de profilés à 5 axes était un argument contre les centres d’usinage de profilés. Une unité d’entaillage ou de fraisage en façade est disponible en plus de deux modules de coupe sur le modèle +Quadra, ce qui offre un degré de liberté supplémentaire. Grâce aux nouveaux supports de profilé réglables par servomoteur de l’Emmegi +Quadra, il est pratiquement inutile de procéder à des modifications manuelles sur différentes séries de profilés dans le magasin de chargement. La machine se règle automatiquement sur le type de profil suivant. Une fabrication automatisée est ainsi possible à partir de la taille de série unitaire.
Solutions spécifiques au client dans un troisième temps
Sur les grandes séries, des couches fantômes complètes sont notamment exigées sans intervention de l’opérateur. L’étape d’automatisation suivante nécessite donc le traitement autonome de la ceinture de profilé jusqu’au produit fini palettisé. Ces exigences sont très spécifiques au client et sont résolues à l’extérieur de la machine à l’aide de robots ou de portails de surface. Emmegi ne restreint délibérément pas le choix du partenaire d’automatisation afin de pouvoir collaborer avec des partenaires locaux de longue date des clients.
Le maître mot : automatisation hybride ou modulaire. L’automatisation supplémentaire est utilisée pour traiter de grandes séries en équipes fantômes. Les profilés ou prototypes complexes et difficiles à manipuler peuvent toutefois toujours être chargés et déchargés manuellement sur la machine. Les lignes de fabrication rigides, qui doivent faire l’objet d’un ajustement chronophage pour les nouvelles séries de profilés, sont rarement efficaces.
Les solutions proposées varient en fonction du type de machine. Les interventions sur les machines à portique 5 axes comme l’Emmegi Satellite XTE sont possibles, mais nécessitent toujours des interfaces professionnelles afin d’ajuster la position des pièces à usiner et des composants mobiles des machines. Emmegi utilise des interfaces de communication classiques telles que Profinet ou DeviceNet à cet effet.
Le centre d’usinage Emmegi +Quadra est également une plate-forme flexible et performante pour ce niveau d’automatisation élevé. Contrairement aux machines à 5 axes, les points de chargement et de déchargement sont statiques. Il n’existe pas de points de collision avec des unités d’usinage, ce qui donne lieu à des solutions plus simples et plus rentables. Enfin, ces machines sont des bêtes de somme qui ont été conçues de fond en comble pour assurer la sécurité des processus en équipes. C’est l’exigence qui définit la solution.
Conclusion
Les approches de l’industrie 4.0 sont déjà bien avancées dans la construction métallique et de façades grâce à l’utilisation de connexions de machines logicielles de construction métallique. Après l’automatisation des processus, la ligne de production suivra dans de nombreux cas.
Une analyse détaillée au sein de l’entreprise est indispensable. Il n’existe pas de solution standard, tout et sur mesure. Une automatisation hybride peut toutefois permettre un fonctionnement sur des périodes plus longues d’exploitation sans opérateur, voire en équipes fantômes, même sans grandes séries.
www.bider-hauser.ch