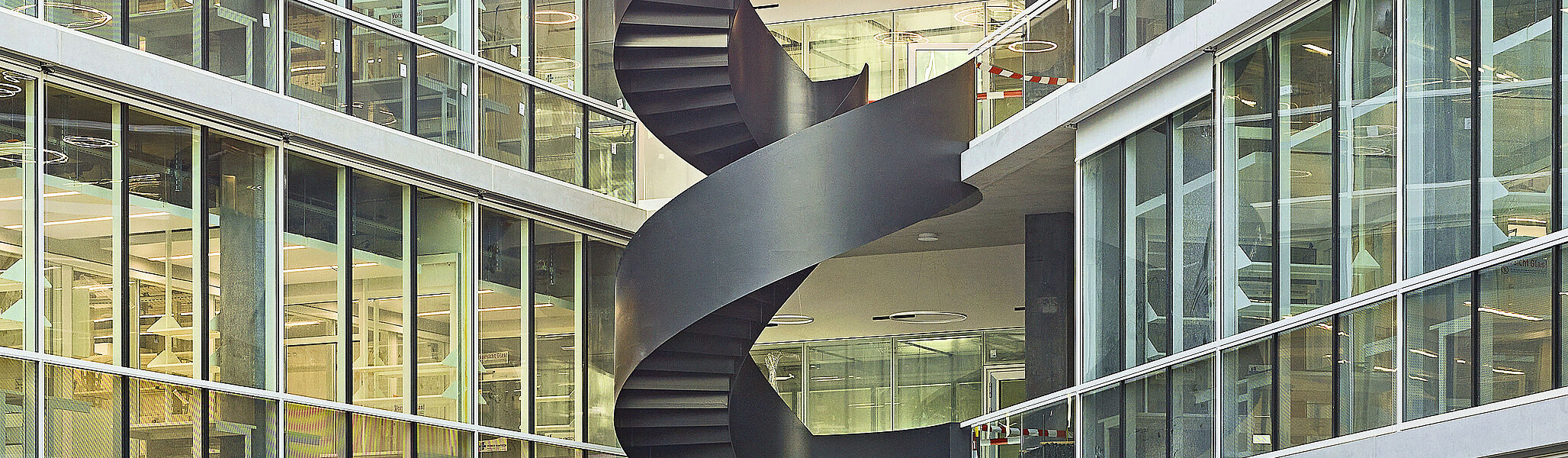
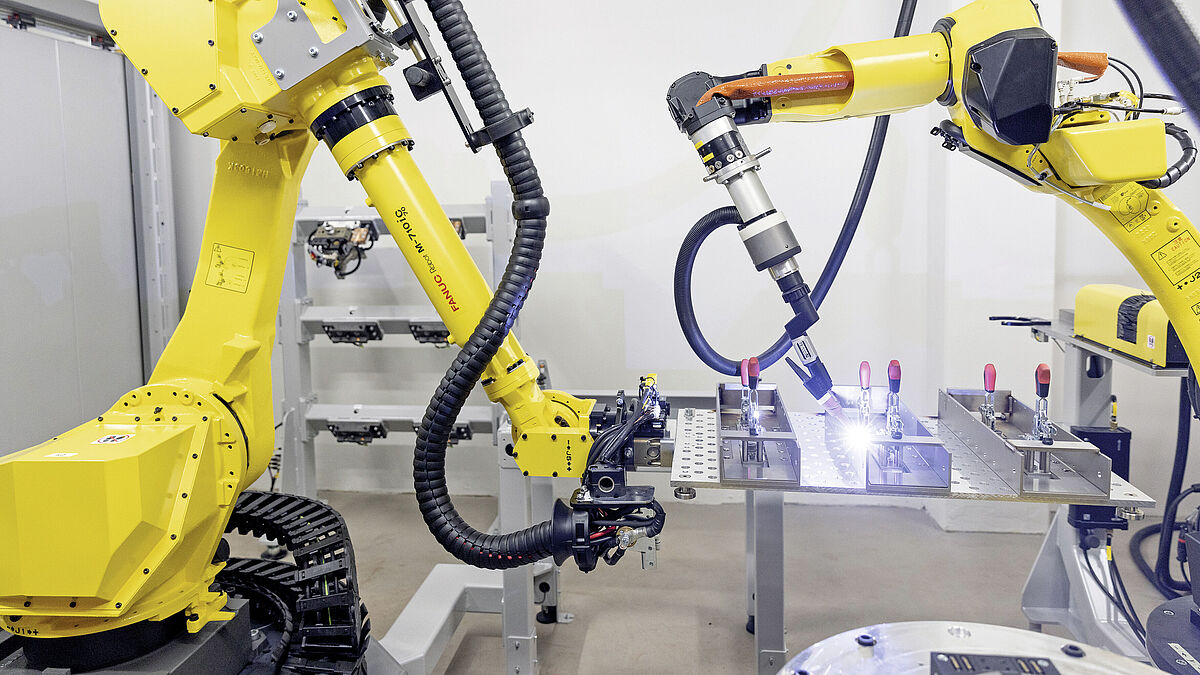
Parés pour l’avenir grâce aux techniques de soudage robotisées intelligentes
Soudage
Progrès et innovation en dialogue avec le client : l’entreprise phare autrichienne Anton Paar fabrique des appareils de mesure ultra-précis pour de nombreux secteurs. Son équipe engagée de chercheurs, ingénieurs et agents de production ont pour ambition de repousser toujours plus loin les limites du possible. Aujourd’hui, Anton Paar GmbH est leader du marché mondial pour les mesures de densité et de concentration, la rhéométrie et la détection de CO 2 dissous. Face à la pénurie croissante de main d’œuvre et à la hausse permanente des quantités produites exigeant des solutions de production intelligentes, l’entreprise a investi dans une cellule de soudage robotisé dernière génération. (Texte sous forme abrégée)
Connexion
Merci de l’intérêt que vous portez à nos contenus. Les abonnés de la revue spécialisée metall trouveront le Login pour l’accès intégral dans les informations légales de la version imprimée actuelle. Le mot de passe change tous les mois.
Inscrivez-vous maintenant pour lire cet article. Inscrivez-vous pour lire les différents articles et payez très facilement par carte de crédit. (CHF 5.- par article)
En tant qu’utilisateur enregistré, vous pouvez accéder à tout moment à l’article acheté.
Si - en tant que professionnel dans les domaines de la construction métallique, en acier et de façades - vous n’êtes pas encore abonné à la revue spécialisée metall, ne perdez plus une seconde et souscrivez dès à présent votre abonnement ici.
Soudage
Parés pour l’avenir grâce aux techniques de soudage robotisées intelligentes
Progrès et innovation en dialogue avec le client : l’entreprise phare autrichienne Anton Paar fabrique des appareils de mesure ultra-précis pour de nombreux secteurs. Son équipe engagée de chercheurs, ingénieurs et agents de production ont pour ambition de repousser toujours plus loin les limites du possible. Aujourd’hui, Anton Paar GmbH est leader du marché mondial pour les mesures de densité et de concentration, la rhéométrie et la détection de CO 2 dissous. Face à la pénurie croissante de main d’œuvre et à la hausse permanente des quantités produites exigeant des solutions de production intelligentes, l’entreprise a investi dans une cellule de soudage robotisé dernière génération. (Texte sous forme abrégée)
Auparavant, tous les composants des appareils de mesure et de réglage produits à Graz étaient soudés à la main. En effet, pour les lots de petites tailles, entre 1 et 400 unités, des installations de soudage robotisé semblaient peu rentables. Les hausses permanentes du chiffre d’affaires, la pénurie de main d’œuvre croissante sur le marché du travail national et les technologies robotisées innovantes – qui rendent désormais le soudage automatique rentable, même sur des lots de petite taille – ont conduit l’entreprise high tech à investir dans une installation de soudage robotisé moderne. Les spécialistes de la mesure et du réglage exigeaient une rentabilité élevée associée à de la flexibilité à tous les niveaux : pour le nombre, la forme et la taille des composants, pour leur positionnement et pour l’utilisation de différents modes opératoires de soudage.
Dominik Santner, COO d’Anton Paar GmbH, souligne : « La pénurie de main d’œuvre et la hausse permanente des quantités produites requièrent de nouvelles solutions dans la production. Cette nouvelle cellule de soudage robotisé représente un grand pas dans l’automatisation de notre production. Si nous avions continué à souder manuellement nos capteurs de production, nous aurions eu beaucoup de mal à atteindre les quantités de pièces prévues dans les années à venir. »
Autonomie de soudage et diversité des composants
Dès le début, les experts d’Anton Paar ont misé sur l’autonomie de l’installation : une fois équipé, le système de soudage devait être en mesure d’exécuter un ordre complet du début à la fin, en une seule fois – par exemple le soudage d’un lot de différents objets, comme un boîtier d’oscillateur, un support principal ou des dispositifs de contre-refroidissement. Le tout en autonomie parfaite, sans intervention des spécialistes du soudage.
Des composants différents par leur forme, leur poids et leur taille, diverses options de prise en main, de positionnement et de dépose, la possibilité d’utiliser deux modes opératoires de soudage (TIG et MIG/MAG) pour un même composant, ainsi que l’utilisation nécessaire de gaz de formation avec les corps cylindrique pour protéger les composants contre les colorations : tous ces facteurs ont fait que la construction de l’installation fut un défi particulier pour l’équipe d’ingénierie et de programmation.
« Nous étions à la recherche d’un partenaire fiable, très similaire à nous en termes de précision et de qualité. Il devait être réellement à l’écoute, répondre à nos attentes et proposer des solutions durables. Des solutions qui nous conféreraient des avantages concurrentiels au cours des années », déclare Daniel Moik, Department Manager Joining Technologies. « Fronius International répondait à ces critères de partenariat durable. En collaboration étroite avec nos techniciens, l’équipe de Welding Automation a mis au point une cellule de soudage robotisé conforme en tous points à nos exigences. Par ailleurs, Fronius est disposé à faire évoluer l’installation avec nous et à l’adapter à de nouveaux besoins. »
« Nous étions à la recherche d’un partenaire fiable, très similaire à nous en termes de précision et de qualité. Il devait être réellement à l’écoute, répondre à nos attentes et proposer des solutions durables. Des solutions qui nous conféreraient des avantages concurrentiels au cours des années. »
Synonyme d’efficacité : Fronius Pathfinder
Chez Anton Paar, les nouvelles soudures sont programmées hors-ligne, en dehors du système de soudage, et pas directement sur l’installation comme c’est généralement le cas. Au lieu d’interrompre les opérations de soudage en cours, on continue à souder, ce qui permet d’augmenter la productivité. Pour y parvenir, les techniciens de soudage importent les données CAO des composants des appareils de mesure à souder dans le Fronius Pathfinder ® . On teste ensuite divers scénarios d’assemblage, on définit des séquences de soudage et on les optimise au cours de simulations.
Ces opérations concernent les trajectoires, les angles de placement de la torche de soudage, les déports de la torche dans les coins et toutes les réorientations du robot de soudage. Le Pathfinder détecte les dépassements de la portée du robot, appelés limites d’axes. Comme les opérateurs du logiciel corrigent le lieu de dépose de la pièce à souder et la positionnent à portée du bras du robot de soudage, ils évitent à l’avance de potentielles collisions de la torche de soudage avec différents bords de composants.
Les sources d’erreurs sont détectées en temps utile
Si des corrections de trajectoire sont nécessaires, les points de programmation concernés peuvent facilement être déplacés par glisser-déposer. Si un déplacement jusqu’au composant doit être modifié, les professionnels appuient brièvement sur « Réinitialisation ». Le robot virtuel se rend alors en position de base pour débuter un nouveau déplacement. En mode de fonctionnement réel, il faudrait dégager le robot, ce qui prend du temps, le placer en position de base à l’aide de la commande du robot et redémarrer le processus de programmation. Ayant opté pour le logiciel de programmation et de simulation hors-ligne Pathfinder, les experts d’Anton Paar gagnent non seulement un temps précieux pour les opérations de soudage, mais peuvent aussi détecter au préalable les sources d’erreurs.
Dès qu’un programme de soudage est terminé dans le Pathfinder, il est traduit dans le code spécifique au robot de soudage Fanuc par un post-processeur. Il peut alors être envoyé à l’installation de soudage par transfert de données – par exemple via une connexion LAN. La fonction « Détermination de la durée de cycle », qui tient compte des vitesses de soudage, des temps de pré-débit de gaz et de remplissage des cratères finaux, constitue un point fort du système et une aide efficace pour toute la planification de production. Par rapport à la programmation avec la commande du robot, le Pathfinder permet d’économiser jusqu’à 90 % de temps – en fonction de la géométrie des composants et des exigences en termes de techniques de soudage.
Sur mesure
Pour souder ces nombreux composants différents, Anton Paar dispose de flux de travail qui lui sont spécifiques, dont les 3 flux principaux qui illustrent parfaitement la flexibilité énorme en termes de diversité de composants.
Flux de travail 1 : Les composants sont soudés sur le manipulateur. On retire une palette chargée de composants du rayonnage à palettes et on la dépose sur un plateau de réception. Par la suite, le robot de manipulation prépare une pince adaptée pour récupérer les composants. 6 pinces différentes sont rangées dans ce que l’on appelle une « gare à pinces ». Une fois équipé, le robot de manipulation récupère les composants et les fixe dans un dispositif de blocage spécifique, déjà placé sur le manipulateur. Les composants sont toujours pris l’un après l’autre, puis soudés et replacés sur la palette.
Flux de travail 2 : Les composants sont soudés immédiatement sur les palettes. Le robot de manipulation transporte les palettes en dehors du rayonnage à palettes et les positionne devant le robot de soudage. Pendant le soudage, le robot de manipulation et le robot de soudage peuvent alors exécuter ensemble des mouvements coordonnés et réaliser ainsi des soudures simples, mais aussi des soudures à géométrie complexe.
Flux de travail 3 : Les composants sont récupérés individuellement, amenés en position par le robot de manipulation et se déplacent de manière synchronisée av ec le robot pendant le soudage (Coordinated Motion).
Pour que l’installation sache quoi faire
Abgesehen von der innovativen Fronius-Schweisstechnologie, den Steuerungen, der Tool-Center-Point(TCP)-Vermessung, der Brennerreinigungsstation und der Einhausung besteht die Roboterschweissanlage aus sieben Kernmodulen, die softwaregesteuert kollaborieren: einem Handling-Roboter, einem Schweissroboter, einem Dreh-Kipp-Positionierer mit Formiergaseinheit, einem Palettenlager mit zwei Regalen, einem Greiferbahnhof, einem Brennerwechselsystem und einer Palettenablage im Inneren der Anlage.
www.fronius.com
Vous pouvez retrouver l'intégralité du texte ici ■