
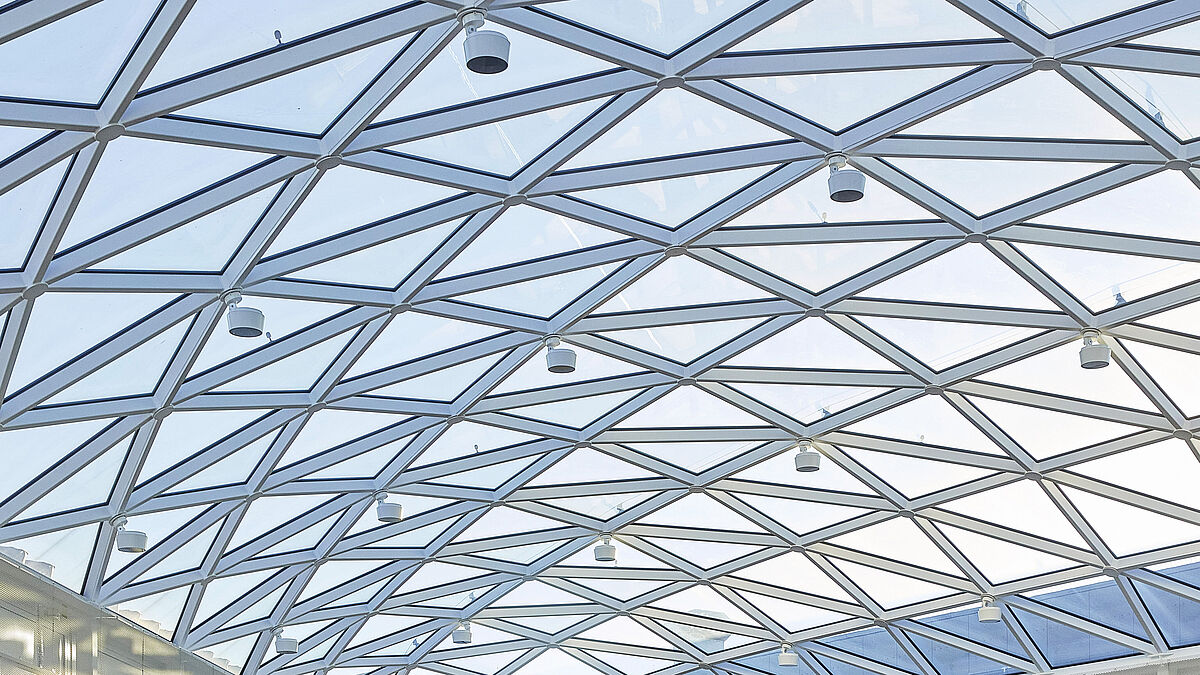
Le secret : les nœuds de jonction
Construction métallique : toit vitré autoportant à structure en treillis
Le patio du bâtiment de laboratoires et de recherche de six étages de l’EPF Zurich à Bâle a été surmonté d’un toit à structure en treillis unique en métal et en verre. La structure se distingue non seulement par ses particularités statiques, mais aussi par les 239 verres triangulaires différents ainsi que par les nœuds de surfaces frontales novateurs.
Connexion
Merci de l’intérêt que vous portez à nos contenus. Les abonnés de la revue spécialisée metall trouveront le Login pour l’accès intégral dans les informations légales de la version imprimée actuelle. Le mot de passe change tous les mois.
Inscrivez-vous maintenant pour lire cet article. Inscrivez-vous pour lire les différents articles et payez très facilement par carte de crédit. (CHF 5.- par article)
En tant qu’utilisateur enregistré, vous pouvez accéder à tout moment à l’article acheté.
Si - en tant que professionnel dans les domaines de la construction métallique, en acier et de façades - vous n’êtes pas encore abonné à la revue spécialisée metall, ne perdez plus une seconde et souscrivez dès à présent votre abonnement ici.
Construction métallique : toit vitré autoportant à structure en treillis
Le secret : les nœuds de jonction
Le patio du bâtiment de laboratoires et de recherche de six étages de l’EPF Zurich à Bâle a été surmonté d’un toit à structure en treillis unique en métal et en verre. La structure se distingue non seulement par ses particularités statiques, mais aussi par les 239 verres triangulaires différents ainsi que par les nœuds de surfaces frontales novateurs.
Sur le campus de l’université de Bâle, un bâtiment de laboratoires et de recherche du Department of Biosystems Science and Engineering (D-BSSE) de l’EPF Zurich a vu le jour. Un patio inondé de lumière dont le sommet est fermé par un toit vitré hautement transparent attire tous les regards.
Le toit vitré autoportant exempt de sous-tirants et de poteaux se compose d’une structure doublement voûtée d’environ 20 m de large et 35 m de long. Les croisements qui en résultent forment des éléments triangulaires aux angles de joints les plus variés. La structure doublement voûtée avec une flèche de 3,0 m permet un toit autoportant, sans piliers, mais extrêmement filigrané. Le premier du genre en Suisse.
Charpente de toit reposant sur un anneau de pression
Le toit vitré à la structure voûtée vers l’extérieur repose sur un mur de soubassement en béton. Une poutre périphérique en acier est montée sur celui-ci et sert de culée à la structure du toit. Des éléments de fenêtres périphériques reposent sur cette « structure à jambette » surélevée.
La poutre horizontale périphérique crée un anneau de pression dont la forme se rapproche de celle d’un triangle scalène aux angles arrondis. Elle forme le cadre et, par conséquent, la base de la charpente de toit. Toutes les charges sont transmises à l’allège mentionnée précédemment via cet anneau de pression. En raison des lignes droites disposées sur les trois côtés, une solution en traction n’était pas possible. Toutefois, la structure en treillis soudée neutralise une grande partie de la poussée horizontale, rendant les charges horizontales correspondantes insignifiantes.
Solutions innovantes requises
Fermer le patio avec un toit vitré aussi léger que possible conformément à la vision de l’architecte et en faire un ouvrage resplendissant a nécessité beaucoup d’innovation et de savoir-faire technique. Des exigences abondamment présentes au sein de l’entreprise mandatée, Ruch Metallbau AG, à Altdorf, spécialisée dans la planification, la fabrication et le montage de structures hors du commun en acier, métal et verre.
« À l’origine, il était prévu que les points de croisement des profilés en acier soient réalisés à partir de nœuds fraisés individuellement et adaptés à la géométrie », explique à « metall » Andreas Ruch, président du conseil d’administration et responsable des « projets spéciaux » chez Ruch Metallbau AG. Et d’ajouter : « Il fallait en outre que la structure de toit se compose d’une construction primaire et d’une construction secondaire pour la structure vitrée en aluminium.
Comme les quelque 240 vitres triangulaires sont toujours agencées selon des angles d’appui différents et que les profilés porteurs se rejoignent selon des angles différents, nous avons décidé de repenser la construction prescrite et de l’adapter à nos besoins. Nous sommes ainsi parvenus à réaliser deux optimisations significatives qui caractérisent cet ouvrage. Il s’agit, d’une part, du nœud de surfaces frontales innovant pour ouvrages porteurs en treillis développé et breveté par nos soins et, d’autre part, de la possibilité qui en découle de renoncer à une structure secondaire pour la structure vitrée. Deux optimisations qui ont débouché sur de nombreux autres avantages aux répercussions positives sur les plans technique et économique. Last but not least, les éléments d’éclairage ronds choisis par les architectes ont ainsi pu être fixés parfaitement aux nœuds nouvellement conçus et y être raccordés. »
« Nous sommes ainsi parvenus à réaliser deux optimisations significatives qui caractérisent cet ouvrage. Il s’agit, d’une part, du nœud de surfaces frontales innovant pour ouvrages porteurs en treillis développé et breveté par nos soins et, d’autre part, de la possibilité qui en découle de renoncer à une structure secondaire pour la structure vitrée. »
Nœud de surfaces frontales de conception nouvelle
Comme indiqué plus haut, le nœud de surfaces frontales breveté par Ruch constitue le cœur de l’ouvrage porteur en treillis. La particularité de ce procédé non conventionnel réside dans le fait que, pour chaque nœud, un cylindre en acier non traité constitue le centre des raccords de profilés. Le manteau du cylindre agit comme surface frontale homogène. Tous les composants géométriques créés sont repris par les tubes rectangulaires usinés différemment par le laser à tubes 3D de l’entreprise. Les profilés creux en acier S355 J0 usinés précisément et numérotés, mesurant 140 x 80 x 6,3 mm, ont été assemblés, collés et soudés simplement en usine sur les cylindres préalablement positionnés dans l’espace. Il était hors de question de procéder à de longues adaptations par ajustements, rectifications ou autres.
Priorité absolue à l’étanchéité du vitrage
Pour que l’ouvrage porteur en treillis serve de base à un vitrage totalement étanche, les tubes en acier profilés reliés aux cylindres ont été découpés de manière très spéciale avec un laser 3D, de sorte que les surfaces d’appui des vitrages se réunissent en pointes sur les points centraux des cylindres et puissent être soudés.
Les caoutchoucs d’appui des vitres (système RAICO SI Therm 56 avec trois niveaux d’étanchéité) ont pu ainsi être amenés sans autre traitement jusqu’au centre du nœud ou du cylindre puis collés ensemble. La qualité de ces endroits exigeants a été surveillée et documentée en vue d’une sécurité de processus élevée.
Les 239 segments vitrés ont été réalisés sous forme de vitrages isolants triangulaires, à appuis linéaires de tous les côtés et avec joints au-dessus. Ils sont accessibles afin de pouvoir être nettoyés (pour de plus amples informations sur le sujet, voir l’article spécialisé « Vitrages accessibles et praticables » de l’édition de novembre 2021).
Les éléments vitrés présentant une superficie allant jusqu’à 3,5 m² et des longueurs de côtés de 3,0 m maximum affichent tous des dimensions différentes et se distinguent donc par leurs formes. Pour la couverture du toit, c’est un double vitrage isolant de protection solaire présentant un angle de montage de 5°, une valeur Ug de 1,6 W/m2K et une valeur g de 0,36 qui a été utilisé. La fixation a été effectuée au moyen de profilés en U dans le joint périphérique. L’étanchéité extérieure est assurée par un joint SG de grande qualité.
Concernant la sécurité structurale des éléments en verre, la capacité de charge résiduelle en cas de bris de verre de plus de 60 heures a été démontrée. Pour ce test, Ruch a prélevé un élément partiel de la structure en acier, a monté le support en caoutchouc et a posé les vitres correspondantes. Une fois le test et l’enregistrement des données réussis, l’élément de test en acier a été réintégré à la construction.
Exigences statiques élevées
Sur une surface de forme libre sans piliers d’une telle taille, les exigences statiques sont maximales. Les exigences strictes des ingénieurs ont dû être respectées et documentées précisément dans tout le processus de réalisation. En tant que partenaire de RUCH Metallbau AG, l’entreprise formTL, de Radolfzell, a pris en charge la modélisation en 3D et la planification de la coordination afin de garantir une reprise continue des données depuis le projet jusqu’à l’assemblage, en passant par le laser à tubes 3D. L’entreprise formTL était aussi en charge de la planification du travail en atelier et du montage ainsi que des contrôles statiques nécessaires à l’exécution.
Sécurité de processus élevée pour la fabrication et le montage
Pour la fabrication et le montage, Ruch Metallbau AG est parvenu à atteindre un très haut degré de préfabrication et, par conséquent, une très grande sécurité de processus. Le toit a été produit et monté élément par élément. Les sept éléments en forme de voile de 4 m de large pour 10 à 21 m de long ont été préfabriqués dans les ateliers de Ruch AG, puis livrés sur chantier par convois spéciaux. Une fois à destination, les grands composants ont été juxtaposés et soudés. Pour ce faire, un échafaudage a été érigé dans le patio afin de créer un niveau de travail approprié. Par rapport aux procédés traditionnels, cela a permis de réduire considérablement les délais de montage, et notamment les travaux de soudage. L’indépendance absolue par rapport aux intempéries, la sécurité de planification, le contrôle de production garanti, la protection anticorrosion et la fiabilité avec laquelle cette commande a pu être exécutée sont d’autres avantages du degré élevé de préfabrication dans les halles de l’entreprise.
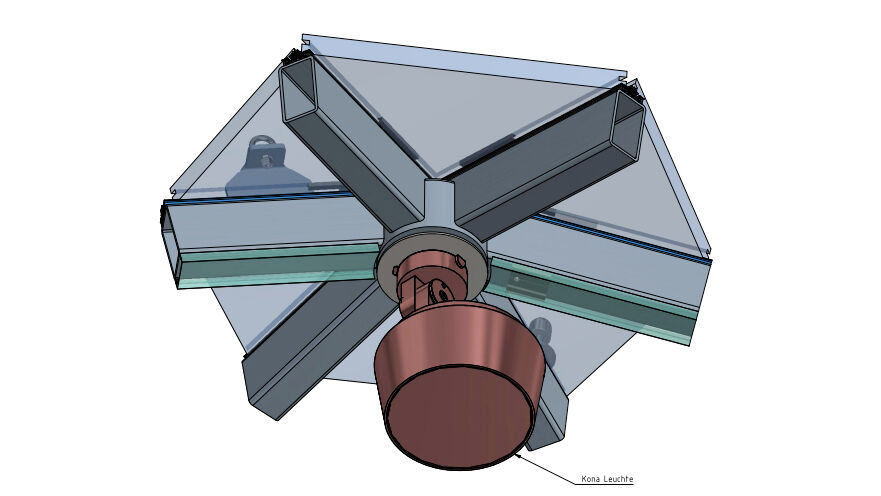
Conclusion
L’ensemble de cette solution innovante caractérisée par une reprise continue des données dans la planification, un nouveau nœud de surfaces frontales breveté et la très grande sécurité de processus dans la production permettront à Ruch Metallbau AG de réaliser dans le monde entier d’autres ouvrages porteurs en treillis de forme libre de grande taille et de qualité optimale. ■
Panneau de chantier
Projet :
Université de Bâle, bâtiment de laboratoires et de recherche du Department of Biosystems Science and Engineering (D-BSSE) de l’EPF Zurich
Maître d’ouvrage :
EPF Zurich
Architecture et planification générale :
Nickl & Partner Architekten Schweiz AG, Zurich
Ingénieur civil :
Leonhardt, Andrä und Partner, Beratende Ingenieure VBI AG, Berlin et Zurich
Construction acier et verre :
Ruch Metallbau AG, Altdorf
Planification de l’exécution :
FormTL Ingenieure für Tragwerk und Leichtbau GmbH, Radolfzell (D)